What is Porosity in Welding: Crucial Tips for Getting Flawless Welds
What is Porosity in Welding: Crucial Tips for Getting Flawless Welds
Blog Article
Recognizing Porosity in Welding: Discovering Causes, Effects, and Avoidance Strategies
As professionals in the welding market are well conscious, recognizing the reasons, results, and avoidance strategies connected to porosity is important for accomplishing robust and trustworthy welds. By delving into the root creates of porosity, analyzing its damaging impacts on weld quality, and exploring efficient prevention methods, welders can enhance their knowledge and skills to create high-grade welds consistently.
Usual Reasons of Porosity
Contamination, in the form of dust, grease, or corrosion on the welding surface, produces gas pockets when warmed, leading to porosity in the weld. Incorrect shielding occurs when the protecting gas, typically made use of in processes like MIG and TIG welding, is not able to completely protect the liquified weld swimming pool from responding with the surrounding air, resulting in gas entrapment and subsequent porosity. Furthermore, insufficient gas insurance coverage, often due to wrong circulation rates or nozzle positioning, can leave components of the weld unprotected, permitting porosity to create.
Results on Weld Top Quality
The existence of porosity in a weld can considerably compromise the overall quality and honesty of the welded joint. Porosity within a weld develops gaps or cavities that weaken the framework, making it a lot more prone to splitting, deterioration, and mechanical failure. These spaces act as tension concentrators, decreasing the load-bearing ability of the weld and boosting the possibility of early failure under applied anxiety. Furthermore, porosity can likewise act as potential websites for hydrogen entrapment, additional aggravating the degradation of the weld's mechanical buildings.
In addition, porosity can impede the performance of non-destructive testing (NDT) strategies, making it testing to detect various other defects or discontinuities within the weld. This can result in considerable security problems, particularly in critical applications where the structural honesty of the bonded parts is paramount.

Prevention Techniques Summary
Offered the destructive influence of porosity on weld quality, efficient avoidance strategies are critical to keeping the structural integrity of welded joints. Additionally, selecting the proper welding specifications, such as voltage, existing, and travel rate, can aid reduce the danger of porosity development. By integrating these avoidance strategies right into welding techniques, the occurrence of porosity see here now can be significantly lowered, leading to stronger and a lot more trustworthy welded joints.
Significance of Proper Shielding
Appropriate protecting in welding plays a critical duty in avoiding climatic contamination and guaranteeing the honesty of bonded joints. Securing gases, such as argon, helium, or a mixture of both, are commonly used to safeguard the weld swimming pool from responding with aspects airborne like oxygen and nitrogen. When these responsive aspects enter into contact with the hot weld swimming pool, they can trigger porosity, leading to weak welds with reduced mechanical homes.

Inadequate shielding can lead to numerous defects like porosity, spatter, and oxidation, compromising the architectural integrity of the welded joint. Adhering to appropriate securing practices is important to create high-grade welds with minimal issues and make sure the longevity and dependability of the welded parts.
Tracking and Control Techniques
How can welders effectively keep track of and control the welding process to guarantee ideal results and protect against defects like porosity? By continuously keeping an eye on these variables, welders can recognize discrepancies from the ideal problems and make instant changes to avoid porosity development.

Furthermore, executing proper training programs for welders is important for keeping track of and controlling the welding process efficiently. What is Porosity. Educating welders on the relevance of maintaining regular specifications, such as correct gas securing and take a trip speed, can assist protect against porosity problems. Regular evaluations and qualifications can likewise make sure that welders are skilled in monitoring and regulating welding procedures
Additionally, making use of automated welding systems can enhance tracking and control abilities. These systems can exactly control welding parameters, reducing the likelihood of human error and making certain consistent weld quality. By incorporating innovative monitoring modern technologies, training programs, and automated systems, welders can efficiently monitor and regulate the welding procedure to reduce porosity flaws Full Report and achieve premium welds.
Final Thought
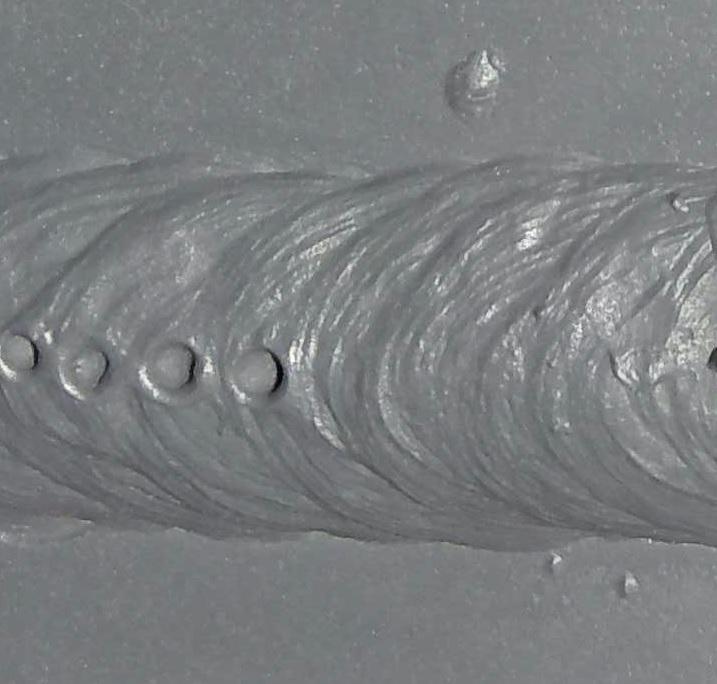
Report this page